On the road toward a more responsible supply chain
September 18, 2017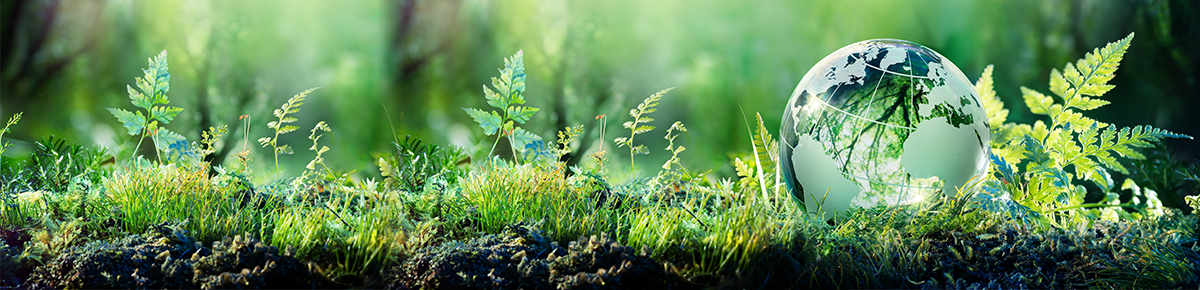
How industry leaders are working to deliver environmental sustainability
BY DENISE DEVEAU
IN today’s environmentally-conscious world, retailers are scrutinizing all aspects of their supply chain activities more than ever before. Managing the transportation side is a key focus for suppliers, fleet managers and retailers alike, from sourcing and distribution centres to storefront and consumer deliveries.
With the proliferation of e-commerce and more demanding customer expectations, the number of transport vehicles on the road has reached unprecedented levels. As growing volumes of products are being transported across the country and throughout the world on a daily basis, many retailers and their partners are exploring new ways to work together to create greater efficiencies and reduce their carbon footprint.
The innovation landscape
Transportation innovation can be found in many facets of operations, from applying the latest technology to gain more visibility and fine-tune forecasting and routing; to implementing tracking tools to reduce fuel consumption and greenhouse gas emissions; to finding more effective ways to reduce packaging and maximize container space.
Logistics, trucking delivery in particular, is going through one of the biggest changes ever, says David Prusinski, Executive Vice President, Sales and Marketing at Fleet Complete in Toronto. “It’s not just how things are done, but the scrutiny being put into the supply chain and the technologies being deployed.”
“THAT’S [E-COMMERCE] BECOMING TABLE STAKES NOW. CUSTOMER EXPECTATIONS ARE HIGHER THAN EVER. HAVING GOOD IN-STOCK POSITIONS AND PICK AND PACK PROCESSES MEANS WE CAN AVOID SPLITTING SHIPMENTS.”
JONATHAN ROSEMBERG
Indigo Books and Music Inc
Not surprisingly, the most advanced transportation innovation is found with larger retailers running larger fleets, he says. “Whether contract or otherwise, a lot have some form of technology to track vehicles, log hours, dispatch, mileage, routing, or vehicle performance.”
For example, advanced sensors and route optimization tools can help fleet managers reduce idling time and save fuel. New asset tracking technology that sends out multiple sensor beams can indicate the actual load of a truck within a few percentage points, allowing fleets to get more efficient usage out of them. Fleet managers for example, can improve load sharing capabilities by dispatching drivers with room to spare to nearby locations to pick up additional loads.
Optimizing for efficiency
Jonathan Rosemberg, Vice President of Strategic Sourcing and Process Improvement for Indigo Books and Music Inc., says it uses third party providers to manage its outbound services. For small parcel delivery to e-commerce customers, the company uses one or two large national carriers, while store deliveries are done by local 3PL providers to gain maximum efficiencies.
“Like everybody else, we are trying to balance how to consolidate as much as possible to minimize costs and our carbon footprint and how many touches are put into the merchandise. At the same time, we need to balance that with the customer experience. That’s kind of the magic act.” He adds that with 210 stores across the country, Indigo has ample opportunities to consolidate shipments.
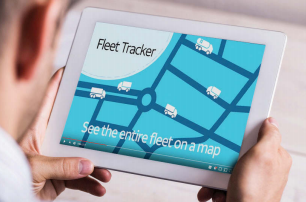
FUTURE THINKING
Future innovation could be something as simple as platooning trucks to reduce wind resistance and greenhouse gas emissions, or alternative energy, Fast says. “At some point compressed natural gas will make a lot of sense. We have to think about where we can start that type of application in our fleet and scale in a way that makes sense.”
The industry is far from idle in moving forward on the process and technology front, Rosemberg stresses. “GPS tracking, and self-driving and electric vehicles will be big industry disruptors over the next 10 to 15 years. The whole industry will be put to the test.”
AI (artificial intelligence) will also play a role, he believes. “With AI, you will have predictive models that will allow you to run a business even more efficiently. Ultimately, self-driving trucks and AI will shift the paradigms of how retailers will manage their supply chains. Sustainability isn’t just about finding suppliers who use electric trucks. The opportunity may be way up higher in the supply chain. You can’t look at transportation in isolation. It’s a whole system—so systems thinking is the way of the future.”
Perhaps one of the biggest challenges facing the e-commerce side of retail is the growing demand for same or next day delivery. “That’s becoming table stakes. Customer expectations are higher than ever. Having good in-stock positions and pick and pack processes mean we can avoid splitting shipments.”
When selecting carriers, Rosemberg says Indigo has an established set of criteria around expectations relating to compliance with Canadian regulations, as well as environmental and sustainability policies. “We want to make sure that any supplier we use manages their carbon footprint in the best and most efficient way possible. We ask questions like: What does their fleet look like? Are the vehicles old or new? How efficient are they on the road?”
“COST PER MILE, COST PER CUBE—THESE ARE THE MEASURES THAT DRIVE US. WE’RE CONSTANTLY LOOKING AT WHAT INNOVATIONS ARE POSSIBLE.”
GARY FAST
Canadian Tire Corporation
Rosemberg notes that carbon footprint reduction and cost savings have now reached a welcome meeting point. “One supports the other. Incentives over the past 12 to 15 years have started to align in a very significant way. Now I find that suppliers that are at the forefront of social and sustainable practices can offer the most competitive pricing.”
A major focus for Indigo these days is planning and allocation, he says. “Technology allows us to forecast demand much more accurately as we get a better understanding of what our customers look like. Through that level of demand management, we can reduce the number of shipments on the road and deliver the best value. The better you are at demand management, the more efficient you can be across the board.”
WALMART GOES BIG ON EMISSION REDUCTION
Walmart has long been among the leading retail players pursuing a sustainable agenda, from reducing packaging and diversion of waste from landfill, to the use of renewable energy and greenhouse gas (GHG) emission reduction.
Since Walmart established a goal to reduce emissions in 2005, it has eliminated a total of over 40 million metric tonnes of emissions throughout its global supply chain, reports Micah Ragland, Director, Sustainability Communications for Walmart.
Walmart’s newest effort is Project Gigaton, a global plan to reduce emissions by one gigaton (1 billion metric tonnes) by 2030. That is the equivalent of removing more than 211 million passenger vehicles in a year, according to the U.S. Environmental Protection Agency’s greenhouse gas equivalency calculator. While the emissions mandate spans many aspects of operations, transportation innovation is a key component in meeting the company’s latest sustainability goals, Ragland says.
Brandon Schott, Manager, Continuous Improvement, Transportation, for Walmart Canada, says Canadian operations are one of 27 global operations involved in achieving the project’s goal. “We will do our best to meet it by continuing to focus on fleet efficiency, and expanding efforts around equipment and alternative fuels.”
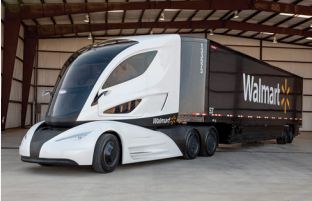
Walmart has been working on a number of initiatives in its quest for continuous improvement, including:
• Advanced systems to improve routing efficiencies and optimize frequency and load fills in order to reduce empty miles and increase utilization
• A trial program in Ontario and Alberta with super cube (60 foot) trailers which increases capacity per load and reduces emissions by up to 14 per cent
• Deploying dual 53-foot LCVs (long combination vehicles) on delivery routes between Mississauga and Cornwall, which reduces GHG emissions by up to 40 percent
• Implementing 105 km per hour speed limit and automatic transmissions in all trucks to improve fuel efficiency
• Equipping all trucks with GPS and telematics capabilities
• Installing battery operated auxiliary power units in trucks to heat cabs in order to minimize idling in winter
• Establishing anti-idling rewards programs for drivers
“We’re also paying close attention to alternative fuels,” Schott says “Right now all of our vehicles are running on diesel, but we are testing fully electric shunt trucks in the trailer yards, and are watching Tesla closely to see what’s going on in the electric vehicle market. We expect to see the first electric tractors hit the market in the next 24 to 36 months.”
Mastering movement on the road
Canadian Tire has a long history of investing in supply chain sustainability and has an extensive combined dedicated and third-party fleet for handling urban and cross-country deliveries. “Anything we need to do in a tight circle—say within a 150 kilometre radius—we will try to tackle with our own fleet,” says Gary Fast, Associate Vice President, International Transportation. “Beyond that, we have some dedicated fleets where service providers domicile their offices and tractors at our distribution centres.”
Initiatives on the drawing board, run from the basic to the advanced, Fast says. “Some gains are achieved through technology, some through process improvement, and some through innovation.”
Given its national scope, backhaul is an integral part of improving efficiency on the road, he explains. “In more remote regions, we often look for backhaul opportunities with vendors once we’ve done a store delivery so the driver has very few empty miles.”
He notes that the amount of cubic feet per load on outbound shipments is a key measure. “Cost per mile, cost per cube—these are the measures that drive us. We’re constantly looking at what innovations are possible.” One of those is route optimization software that converts orders to cubic feet and allows planners to minimize miles for drivers while optimizing loads.
In addition, anything going to stores or coming offshore is floor loaded, adding almost double the capacity to shipping containers. “The further the distance you travel, the greater the savings,” Fast says.
In some instances, Canadian Tire has converted to 60-foot containers versus the standard 53-foot, size. “That doesn’t sound that innovative, but adding those extra feet is a game-changer for us because we gain a net 13 per cent increase in capacity,” Fast notes.
One of its biggest innovations on the road has been longer combination trailers. “When we introduced those in 2009, we were the first carrier in Ontario to do it,” he says.
Forecasting is equally critical in ensuring transportation efficiency, he adds. “Analysts work with merchants to forecast to the SKU level 26 weeks ahead. The software transmits that data to our suppliers and vendors for loading into their MRP [material requirements planning] system. Store deliveries are also based on our forecasts. That kind of supply chain visibility is critical. Simply put, the more data and ability to measure, the greater the visibility and efficiency.”